適正製造規範(GMP)とは、食品の安全性を確保するために守るべき最低限の基準です。これを遵守することで、消費者に安全な食品を提供できます。具体的には、製造工程や施設、従業員の衛生管理が重視されます。
適正製造規範の重要性は、食品の安全性に関するデータにも明らかです。例えば、世界保健機関(WHO)によれば、毎年約6億人が食品による感染症に罹患し、42万人が死亡*1しています。これらの問題は、GMPの遵守によって防ぐことができます。
具体例として、工場内の衛生管理が適切でないと、食品への細菌やウイルスの混入が起こり得ます。これが原因で食中毒などの健康被害が発生する可能性があります。また、製品に記載されている原材料以外のものが混入することも、適正製造規範を守らない場合のリスクです。例えば、アレルギーを持つ人にとっては、原材料に記載のないアレルゲンが混入することは、重大な健康被害につながります。
本記事ではGMPについて、詳しく解説していきます。
*1 WHO’s first ever global estimates of foodborne diseases find children under 5 account for almost one third of deaths(https://www.who.int/en/news-room/detail/03-12-2015-who-s-first-ever-global-estimates-of-foodborne-diseases-find-children-under-5-account-for-almost-one-third-of-deaths)
GMP(適正製造規範)とは
適正製造規範(GMP)とは、製品の品質と安全性を確保するために守るべき基準であり、製造業界における品質管理の基盤です。その目的は、消費者に安全で信頼性の高い製品を提供することです。
GMPの歴史は、1960年代にアメリカで薬品の品質管理が求められるようになったことに始まります。その後、世界保健機関(WHO)がGMPの国際的な基準を策定し、各国がそれに基づいて独自のGMPを導入しました。これにより、製品の品質と安全性が国際的に保証されるようになりました。
適正製造規範(GMP)は、製品の品質と安全性を確保するための重要な基準であり、その歴史と国際的な基準によって、消費者に安全で信頼性の高い製品を提供できるようになりました。これからもGMPは、製造業界における品質管理の柱として、さらなる発展が期待されます。
GMPの主要な要素
GMPの主要な要素は、品質管理システム、製造工程の管理、施設と設備、従業員の衛生教育と管理が挙げられます。これらの要素が適切に整備・運用されることで、製品の品質と安全性が確保されます。
品質管理システムは、製品の品質を維持・向上させるための仕組みで、品質方針や目標を明確にし、組織全体で取り組むことが重要です。具体的には、原材料の受け入れから製品の出荷まで、一貫した品質管理を行い、異常が発生した場合には迅速な対応が求められます。
製造工程の管理では、製品の安全性や品質を確保するために、各工程での管理基準や手順が定められ、徹底されることが大切です。例えば、原材料の投入量や温度管理、製造時の衛生状態などが適切に管理されることで、品質のばらつきが抑えられます。
施設と設備に関しては、製造環境を清潔に保つことが求められます。これには、定期的な清掃やメンテナンスが不可欠で、また、設備の改善や更新も適時行われることが望ましいです。
従業員の衛生教育と管理は、製品の安全性を確保するために欠かせない要素です。
従業員には、衛生に関する教育や研修が定期的に実施され、その理解度や適用状況が確認されるべきです。
このように、GMPの主要な要素は、品質管理システム、製造工程の管理、施設と設備、従業員の衛生教育と管理があり、これらが適切に実践されることで、製品の品質と安全性が確保されます。
GMPの実践方法
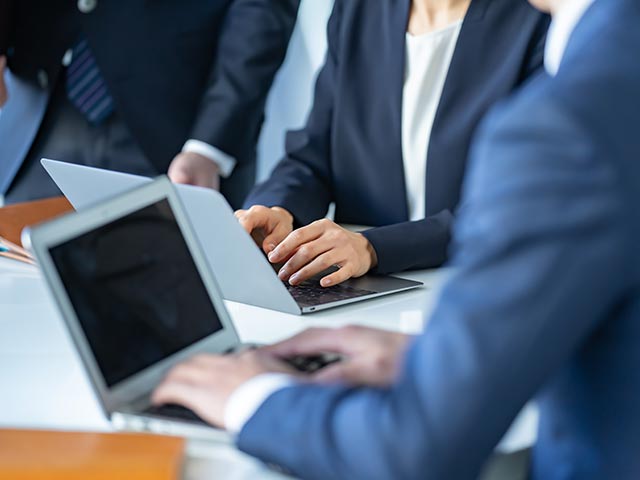
GMPの実践方法は、品質マネジメントシステムの導入、文書化と記録管理、内部監査と改善活動があります。これらを適切に実施することで、製品の品質と安全性が確保されるでしょう。
品質マネジメントシステムの導入は、組織全体で品質を管理し、改善するための仕組みを整備することです。具体的には、品質方針や目標を明確にし、全従業員がその方針に基づいて業務を遂行することが重要です。また、組織内でのコミュニケーションや情報共有が円滑に行われることで、迅速な意思決定や問題解決が可能になります。
文書化と記録管理は、製品の品質保証に欠かせない要素です。
製造工程や品質管理手順を文書化し、適切に管理することで、従業員が手順に従った業務を行い、製品の品質を一貫して維持することが可能になります。また、記録管理を徹底することで、異常が発生した際の原因追及や改善策の立案が容易になります。
内部監査と改善活動は、GMPの継続的な遵守と向上を目指すための重要なプロセスです。
定期的に内部監査を実施し、問題点や改善点を明確にすることで、組織全体の品質向上につながります。また、改善活動によって、問題点の根本原因を解決し、再発防止策を講じることが求められます。
GMPの実践方法は、品質マネジメントシステムの導入、文書化と記録管理、内部監査と改善活動があり、これらを適切に実施することで、製品の品質と安全性が確保されます。
GMPの認証制度
GMPの認証制度は、国内外の認証機関と基準、認証取得のメリットと手順があります。
これらを理解し、適切に認証を取得することで、製品の品質向上や信頼性の向上が期待できます。
国内外の認証機関と基準では、各国で異なるGMP基準が存在し、それぞれの国や地域の法規制や要求に適合した製品を提供するために認証を受けることが求められます。
例えば、日本では日本薬局方*2GMP、アメリカではFDAのGMP基準、欧州ではEU-GMP基準が適用されます。国際的な取引を行う場合には、これらの基準に沿った認証取得が不可欠となります。
認証取得のメリットと手順については、まずメリットとして製品の品質や安全性が向上し、顧客からの信頼も得られることが挙げられます。また、認証取得により国際的な市場での競争力が高まり、新たなビジネスチャンスが広がるでしょう。認証取得の手順は、認証機関への申請、必要書類の提出、現地監査の実施、そして認証の取得と維持が含まれます。継続的な改善と監査を通じて、認証の維持や更新が求められます。
GMPと食品安全法規
GMPと食品安全法規では、適正製造規範とHACCP、日本の食品安全法規とGMPの関連性が重要です。
これらを適切に理解し、実践することで、食品の安全性や品質を確保できます。
適正製造規範とHACCPは、それぞれ異なる目的と方法で食品安全を確保するものです。GMPは、製品の品質を保つために一貫した製造プロセスを確立し、従業員の教育や設備の整備に重点を置いています。
一方、HACCPは、製造工程における危害要因を特定し、それらを制御することで食品の安全性を確保するための管理システムです。GMPとHACCPは互いに補完しあう関係にあり、両者を適切に実施することで食品の安全性と品質が向上します。
一見似ているようにも思えるGMPとHACCPを比較してみましょう。
項目 | GMP(適正製造規範) | HACCP |
---|---|---|
目的 | 製品の品質を保証するための基本的な製造管理手法です。 | 食品の安全性を確保するためのリスク管理手法です。 |
概要 | 製造過程全体を対象にした総合的な品質管理システムです。 | 特定の危害要因を制御することに焦点を当てたシステムです。 |
基本原則 | 衛生管理、製造設備の維持、従業員教育、品質管理など。 | 危害分析、危害要因の特定、対策の設定、監視、検証など。 |
対象産業 | 食品、医薬品、化粧品など多岐にわたる製造業。 | 主に食品業界で使用されています。 |
法的根拠 | 各国の法規制やガイドラインに基づいています。 | Codex Alimentarius(国際食品標準規格)に基づいています。 |
対象 | 製品の製造工程全体を対象としています。 | 主に製品の安全性に関わる特定の危害要因を対象としています。 |
アプローチ | 予防的な管理手法を取り入れた品質管理システムです。 | リスクアセスメントとリスクマネジメントを組み合わせたシステムです。 |
認証制度 | GMP認証を取得することができます。 | HACCP認証を取得することができます。 |
GMPは製造過程全体を対象にした総合的な品質管理手法であり、HACCPは食品の安全性に関わる危害要因を特定・制御するリスク管理手法です。両者は互いに補完しあう関係にあり、食品の品質と安全性を確保するために連携して活用されることが望ましいとされています。
日本の食品安全法規とGMPについては、日本では食品衛生法や食品添加物規制など、食品の安全性や品質を確保するための法規制が定められています。これらの法規制は、GMPの考え方を取り入れることで、製造現場での食品安全管理がより効果的に行われることが期待できます。また、日本薬局方GMPや食品GMP*3(食品製造工程管理基準)など、日本独自のGMP基準も存在し、これらの基準に沿った製造が求められます。
GMPと食品安全法規では、適正製造規範とHACCP、日本の食品安全法規とGMPの関連性が重要であり、これらを適切に理解し、実践することで、食品の安全性や品質を確保できます。
GMP対応の具体的な事例
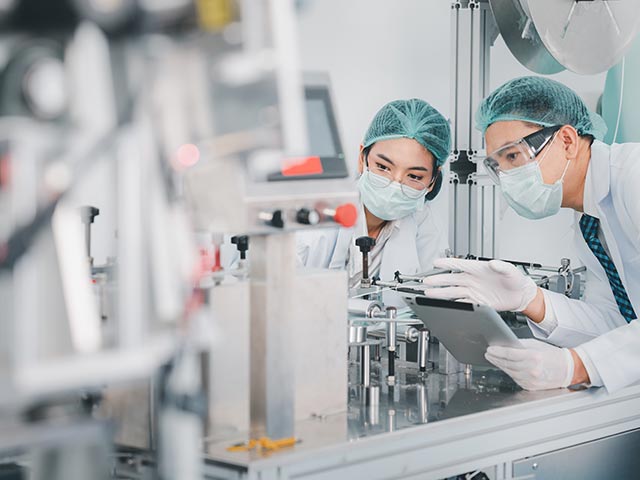
GMP対応の具体的な事例では、適切な衛生管理が防いだ食中毒事例と、GMP導入による品質向上の実例が参考になります。
適切な衛生管理が防いだ食中毒事例においては、従業員の手洗いや設備の清掃・消毒が適切に行われていたことで、食中毒原因の細菌が食品に付着・繁殖することを防いだ実例が数多くあります。このような事例では、GMPに基づく衛生管理の徹底が、食中毒を未然に防ぐ効果を示しています。
一方、GMP導入による品質向上の実例では、徹底した品質管理システムの構築により、製品の安定した品質が確保され、顧客からの評価が高まったケースが報告されています。
具体的には、製造工程の標準化や、従業員教育の充実、設備の改善などが実施され、これにより製品の瑕疵率(欠陥や不備の割合)が大幅に低下し、顧客満足度が向上しました。
このように、GMP対応の具体的な事例を通じて、適切な衛生管理が食中毒事例を防ぎ、GMP導入が品質向上に繋がることが分かります。これらの事例を参考に、自社の食品製造にGMPの考え方を取り入れることで、食品の安全性と品質を向上させることができます。
GMPの今後の展望と課題
GMPの今後の展望と課題については、食品業界のトレンドとGMPへの影響、さらにGMPの普及と発展に向けた取り組みが重要となります。
食品業界のトレンドでは、消費者の健康志向や持続可能性への関心が高まり、食品メーカーによる品質や安全性への取り組みが一層求められています。このため、GMPは今後も食品業界で重要な役割を果たすでしょう。
また、新技術の導入や食品製造プロセスのデジタル化が進む中、GMPの取り組みもこれらの変化に適応していく必要があります。
GMPのさらなる普及と発展に向けては、小規模事業者や新興国での普及が課題となっています。これらの事業者や国々では、資金や技術力の不足がGMP導入の障壁となることが多いため、支援策や情報提供が求められます。また、GMPの国際的な認知と共通基準の整備が進められることで、世界的な食品安全基準の向上に寄与することが期待されています。